Electric Roller Suited for High-Temp Web Applications
Billed as “game-changing” product to enhance process control and efficiency.
Webex’s Electric HTR Roller has been designed to address the unique needs of industries requiring high-temperature applications. It boasts several features that Webex, a Maxcess company, says make it a game-changer for manufacturers looking to achieve precise process control and efficiency.
Key Features of the Webex Electric HTR Roller:
Even Heat Profile: The Electric HTR Roller offers an even heat profile end-to-end, ensuring consistent temperature distribution across the entire roll face, which is essential for high-quality production.
Multiple Heating Zones: With multiple heat zones, the Electric HTR Roller accommodates various web widths, enabling manufacturers to optimize their processes.
Fast Ramp-Up Time: The Electric HTR Roller achieves process temperatures of up to 850°F in approximately 1 hour, significantly reducing downtime and improving overall productivity.
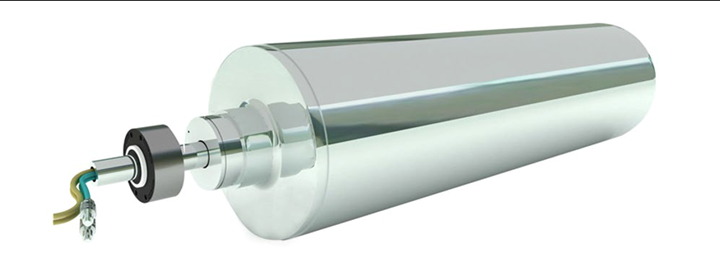
Integrated Zone Temperature Control: Featuring integrated zone temperature control with high alarm shutoff, the Electric HTR Roller offers enhanced safety and precision.
Compatibility: The Electric HTR Roller seamlessly integrates with existing controllers, providing a hassle-free upgrade option for manufacturers. Alternatively, customers can request Webex to supply compatible controllers.
Reduced Maintenance: This environmentally-friendly solution reduces maintenance costs and downtime, offering long-term benefits to users.
Energy Efficiency: The Electric HTR Roller provides up to 70% energy savings compared to traditional fluid-heated rolls, making it a cost-effective choice for businesses.
Notes Jason Annes, global product manager at Maxcess, “The Webex Electric HTR Roller represents a major advancement in the web handling industry. With its precision control, fast ramp-up time and energy efficiency, manufacturers in various industries can expect improved productivity, reduced operational costs and superior product quality.”
Related Content
-
The Importance of Viscosity in Melting
The calculations required to determine the right melt temperature for each polymer are complicated. Knowing the power-law coefficient and the consistency index of the polymer you run might prove useful.
-
Understanding Melting in Single-Screw Extruders
You can better visualize the melting process by “flipping” the observation point so that the barrel appears to be turning clockwise around a stationary screw.
-
Why Compression Ratio is Important
Compression ratios have been pretty much standardized over the years, based on what has typically worked before. But there are quite a few variables that must be considered in order to get the optimum performance from your screw.